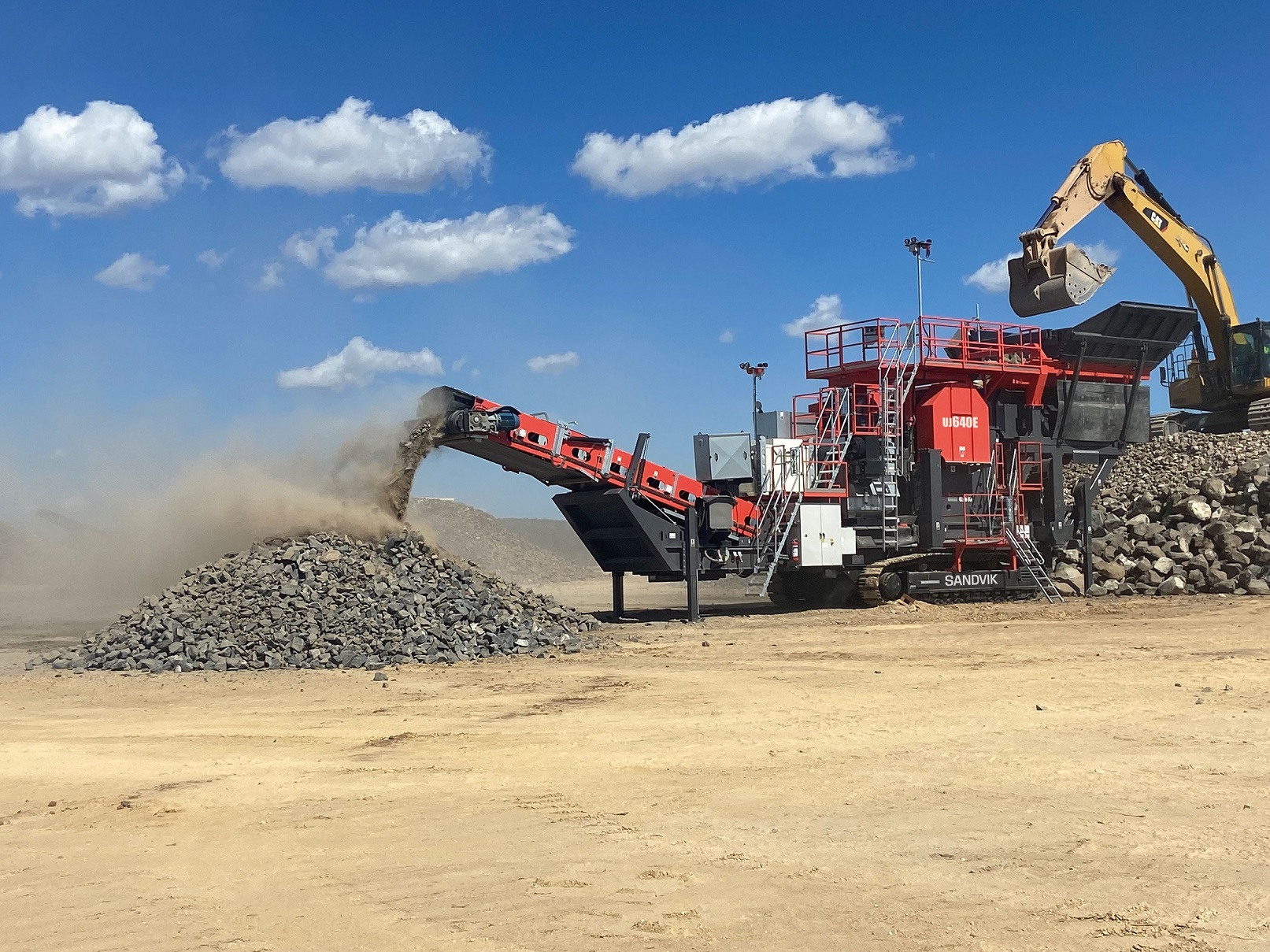
With the experience of Sandvik equipment in a stationary application and recommendations as a supplier of one of the best mobile jaws in the industry, Colorado Materials decided to invest in the largest tracked jaw crusher in the Sandvik mobile crushing and screening offering and haven’t looked back since. They say their first mobile unit of this size, Sandvik UJ640E, which they have aptly named “Goliath”, is one of the best they have seen in 35 years of crushing.
Colorado Materials is one of the largest privately held quarries in the United States. Established in 1980, the Hunter, Texas quarry provides millions of tons of materials annually to various locations via truck and rail. In addition to the main quarry, Colorado Materials, Ltd. maintains several locations across Texas, providing easy delivery to many project locations. As a company, they are committed to providing quality crushed limestone and hot mix asphalt with personalised customer service to their clients throughout Texas.
To process their aggregates, Colorado Materials have been operating Sandvik jaw crushers in a stationary application for several years and is already familiar with the reliability and performance. When a new project came up to process basalt from a mountain in Texas, it was decided that a mobile unit was the best option to reduce the transportation of the material to the crusher. Sandvik Mobiles' local distributor in Texas, Crushing Tigers, was quickly on hand to determine the best model to suit their application. Sandvik was the obvious choice in the selection process.
Due to the high capacity requirements and need for a reliable machine, the tried and tested UJ640E primary tracked jaw crusher was proposed by Crushing Tigers. The biggest in the Sandvik range of portable plant, the UJ640E features a large 60 x 44" / 1500 x 1100 mm single toggle jaw capable of achieving up to 1,100 stph / 1,000 mtph. The machine is well-proven in hard and abrasive rock applications and seemed the ideal fit for Colorado Materials' basalt application.
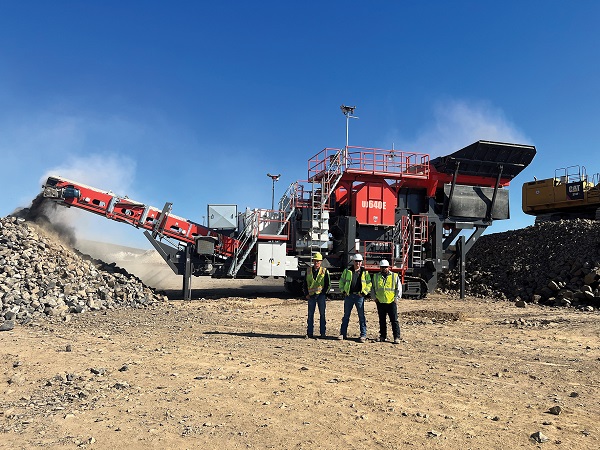
UJ640E电能,提供了一个罗w-cost-per-ton solution. It comes with an onboard diesel generator & electric plug-in grid supply, so customers can choose the most efficient means to operate. This has environmental benefits reducing fuel consumption and carbon footprint and providing cleaner working conditions on-site through less operating noise and emissions. In addition, the unit also comes fitted with a dust suppression system as standard to minimise dust emissions and rubber-lined impact zones for reduced operating noise.
John Janek, operations manager at Colorado Materials, says they have been impressed with the unit's efficiency and that the "fuel economy is excellent for a gen-set."
As well as fuel economy benefits, all onboard components are electrically driven. This improves the reliability of the unit and reduces the overall maintenance required.
Janek says he cannot fault the reliability since commissioning the machine. "Reliability has been excellent, and production rates as expected for the reduction required."
They have been so impressed with the UJ640E that they have decided to move to a Sandvik Mobiles' secondary crushing stage, meaning the jaw can be opened up and capacity substantially increased. During this customer's process, the production capacity ranges from 450-500 stph / 400–450 mph. They are currently reducing to 6" / 150mm minus with a feed size of 30" / 760mm.
Designed with many features to maximise uptime, the Sandvik UJ640E features an 18 yard³ / 14 m³ feeder hopper extension to enable faster loading and provide a continuous feed to the Sandvik CJ615 single-toggle jaw, maximising throughput and efficiency.
Although this mighty unit stands at an impressive 24' / 7.3 m tall during operation and weighs in at 151.5 short tons / 137.5 metric tons, it is easily transportable in just two main sections. These sections are self-supported for easy on-site assembly, resulting in more uptime and higher productivity.
Janek has been in the industry for 35 years and knows about crushing. He praises the UJ640E and adds that it is a "beast of a machine". He says it is a very productive unit, and the engineering design is 10 out of 10. "Durability and engineering of the machine are the best I have seen in 35 years of crushing."
"Whenever the need has arisen for support with training, service or assistance, Crushing Tigers and Sandvik as an OEM have really stood up to the plate. I would not hesitate to recommend Crushing Tigers and the Sandvik brand to anyone in search of crushing and screening equipment."